
Overview
-
BRCKG5-13.8 AC vacuum contactors (hereinafter referred to as: contactor) are applied in power network with AC frequency of 50/60Hz, rated voltage of 13.8kV, and rated current below 800A in the main loop for the remote making and breaking, frequent start and control of AC motor. It is advisable to use them in combination with fuse and protective device to replace vacuum circuit breaker.
Ambient Conditions for Use
-
1 Ambient air temperature is neither higher than +40℃ nor lower than -10℃;
2.2 Altitude of installation site does not exceed 2000m;
2.3 The maximum mean monthly relative air humidity is 90% in the wettest month. The minimum mean monthly temperature is 25℃, with consideration of condensation generated on the surface of product due to temperature change.
2.4 The operating condition shall be free from obvious impact and vibration;
2.5 The medium is without explosion danger, and in the medium there is no gas and dust (including conductive dust) sufficient for corroding metal and destroying insulator.
2.6 The operating condition shall be free from rain and snow.
Model No. & Specification
-
Composition of model No. and meanings:
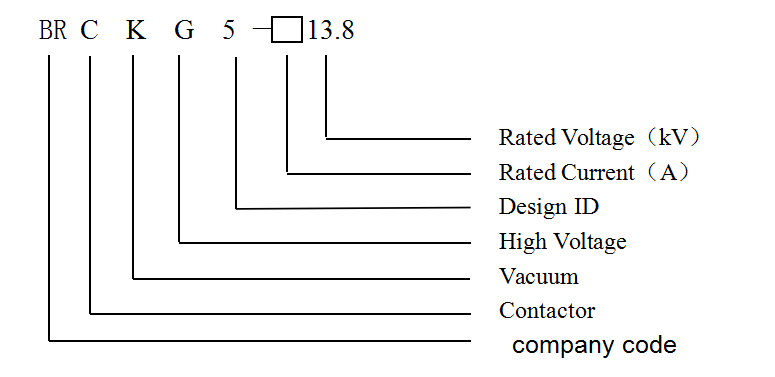
Structure and Operating Principle
-
The contactor consists of base frame, electromagnetic mechanism and vacuum interrupter. Electromagnetic mechanism switches vacuum switch tube via armature, connecting lever and draw bar. Magnet coil is powered on when connected to control power supply. Armature drives connecting lever rotate when closing, causing the moving contact and fixed contact in vacuum interrupter to close up, and the break spring is compressed with energy stored. After closure of moving contact and fixed contact, auxiliary switch connects holding winding in series in the starting winding loop, to throttle the coil and keep magnet closed. If control power supply is disconnected, electromagnetic mechanism is powered off, and break spring is released to separate main contact and main loop breaks.
-
Vacuum interrupter is composed of upper cover, lower cover, metal bellows and ceramic tube. Its enclosure adopts corrugated porcelain tube made up of 95 ceramic. The porcelain tube features long creepage distance, high mechanical strength, heat resistance, impact resistance, etc. A pair of moving contact and fixed contact is sealed in vacuum interrupter. Contact material is Cu - W - Wc, which is of ablative resistance and low diversion closure value. In this way, if the interruption conditions are met, overvoltage caused by cut-off can be reduced in the interruption, so that service life of electric contact can be lengthened. Metal bellows drive moving contact to switch on and off while axially moving.
-
Considering advantages such as good coordination between actual attractive force and spring force characteristics, low-noise and energy saving, DC double coil, made up of starting winding and holding winding, is used for electromagnetic system, which is switched via auxiliary switch. In order to facilitate users to operate AC power supply, contactor is equipped with bridge rectifier.
-
Mechanical padlock can be selected. When closing coil is charged, contactor is closed and mechanical padlock is locked. When trip coil is charged, mechanical padlock is tripped, and contactor is released. In thermal state, if voltage of trip coil is within 85% -110% of its rated voltage, contactor can be reliably released.
Main Technical Parameters
-
1.Overall and installation dimensions (See Fig.1,2)
2.See Table 1 for main technical features;
3.Number of pole of main loop is 3;
4.Control power supply: 220V, 380V and 50Hz/60Hz, and also customized according to user needs;
5.Control loop is DC electromagnet. Coils are connected with AC control power supply via power module. Schematic diagram and wiring diagram (See Fig3);
6.Rated duty: discontinuous long-time duty and repeated short-time duty (rated on-load factor is 40%);
7.The auxiliary contact is three normally open and normally closed two, vheating current is 5A
Installation:
-
1.1Mounting hole is drilled on mounting plate based on dimensions in Fig. 1,2;
1.2It shall be fixed with M8 bolt and lock washer, mounting inclination not exceeding 15 degrees;
1.3Wires of control power supply and auxiliary contact are properly connected to secondary input terminal;
1.4Copper busbar is properly connected to main loop.
1.5Operating voltage and current of main loop and control loop of contactor shall be in accordance with the specifications, in avoidance of damage; -
1.Check if the appearance is damaged. If so ,should stop the usage
2.Clear and get rid of the dirt on its face because of transport of other reasons
3.After installation well ,must be sure that the load switch in off position. If so, insert the operation handle into the grounding holes on its upper board ,then rotate clockwise 180 to switch on the grounding. Anti-clockwise 180 to off the grounding.
4.When go to do the work of switching –on, firstly let the load switch be off position, then insert the operation handle into the operating hole of the load switch in lower board
5.Operating From switch-on to switch off, For K type spring institution: insert the operation handle into the hole of load switch, anti-clockwise rotate 180 to do the off-switch.
For A type spring institution, push the switch-off button to off the switch. Inspect the switch position through its viewing window, and watch its indication comply with the requirements or not.
Check and adjustment
-
2.1For contactor in service, its vacuum degree shall be checked once every half a year (power frequency withstand voltage method). Power frequency withstand voltage of vacuum interrupter of 7.2kV shall be more than 15kV;
2.2Routine check, lubrication and cleaning are performed once a year.
2.3Check if auxiliary contact is well contacted. In case of bad contact, it shall be maintained or replaced;
2.4After operating for 100,000 times, it shall be thoroughly checked.
2.5If vacuum interrupter is seriously damaged or burned, it shall be replaced at once. After replacement with new vacuum interrupter, contactor shall be overall adjusted. Methods: Charge electromagnetic system of contactor to close vacuum interrupter, and check interval between over-travel adjusting nut and washer with self-made insert, which shall be between 1mm and 1.5mm, with three phases being consistent. Measure the distance L1 between the plane 5 of guide sleeve on vacuum tube and the surface of flexible connector at the end of guide rod with measuring tools (inside calipers), and then interrupt and release contactor. Then, adjust separation adjusting screw, to make the distance L2 between the plane of guide sleeve and the surface of flexible connector at the end of guide rod is equal to the sum of L1 and rated separation between contacts, (while adjusting separation, three phases need to be repeatedly debugged, to guarantee synchronism of three phases), and tighten each adjusting nut, thus separation and over-travel are adjusted up (See Fig1).
2.6 Operation tests within the following voltage range shall be performed for the adjusted contactor:
a.Open and close the contactor for 5 times with 85% rated control supply voltage;
b.Open and close the contactor for 5 times with 110% rated control supply voltage;
c.If rated control supply voltage is lower than 30%, contactor must be released and try twice.
Common faults and elimination
-
Table 2 Common faults and troubleshooting
Fault |
Causes |
Corrective measures |
Phenomenon |
||
No closing |
1. Power supply circuit of |
1.Check circuits to find out |
Closing not |
1.Control supply voltage |
1.Adjust supply voltage. |
Excessive |
1.Voltage of control |
1. Adjust control supply |
|
|
|
Excessively |
1.Total separation is too |
1.Adjust separation |
Excessively |
1.Acting force of |
1. Adjust acting force of |
Excessive |
1. Voltage of control |
1. Check voltage of control |
Breakdown |
1. Voltage of control |
1. Check voltage of control |
Table 1 Main technical parameters
Name of Parameter |
BRCKG5-160-630/13.8 |
BRCKG5-800/13.8 |
||||||
160A |
250A |
400A |
630A |
800A |
||||
Main loop |
Rated voltage (kV) |
13.8 |
13.8 |
|||||
Rated current (A) |
160 |
250 |
400 |
630 |
800 |
|||
Making capacity (A/100 times) |
1600 |
2500 |
4000 |
6000 |
8000 |
|||
Making and breaking capacity (A/25 times) |
1280 |
2000 |
3200 |
5000 |
6500 |
|||
Limit breaking capacity (A/3 times) |
3200 |
4000 |
4500 |
6000 |
7000 |
|||
Rated power frequency withstand voltage (kV) |
42 |
42 |
||||||
Service life |
Electrical AC3 (10,000 times) |
30 |
30 |
|||||
Mechanical (10,000 times) |
100 |
100 |
||||||
Operation power supply |
|
40 |
450 |
|||||
Closing |
Starting (VA) |
1000 |
1000 |
|||||
Holding (VA) |
50 |
50 |
||||||
Rated operation frequency AC3 (times/h) |
300 |
300 |
||||||
Short-time operation frequency times/h (20s) |
1000 |
1000 |
||||||
Power frequency withstand voltage of secondary loop (kV) |
2.5 |
2.5 |
||||||
Power frequency withstand voltage of control circuit (kV) |
2 5 |
2.5 |
||||||
Rated operation frequency (times/h) |
300 |
300 |
||||||
Operation frequency of mechanical locking (times/h) |
120 |
120 |
||||||
Closing time (ms) |
≤170 |
≤150 |
||||||
Breaking time (ms) |
≤150 |
≤120 |
||||||
Asynchronous time of three phases (ms) |
≤3 |
≤3 |
||||||
Separation between contacts (mm) |
4±0.5 |
5±0.5 |
||||||
Over-travel (mm) |
≥1.2 |
≥1.2 |
||||||
Resistance of main loop (μ Ω) |
≤200 |
≤200 |
≤150 |
≤100 |
≤80 |
|||
Terminal pressure (N) |
>100 |
>100 |
>120 |
>180 |
>180 |
Storage and Transportation
-
1.Contactor shall be stored in well-ventilated environment with relative humidity less than 85%, and room temperature between -25℃and +40℃.
2.Long-term unused contactor must be regularly checked (once half a year);
3.Working contactor shall be checked by special persons with detail records;
4.During transportation, it is not allowed to have intense vibration and impact, and prevent rain and snow.
Order Information
-
The following contents shall be stated while placing an order:
1.Specification & type of contactor;
2.Rated voltage of contactor;
3.Rated current of contactor;
4.Control supply voltage;
5.Quantity of contactor and that of accessories.
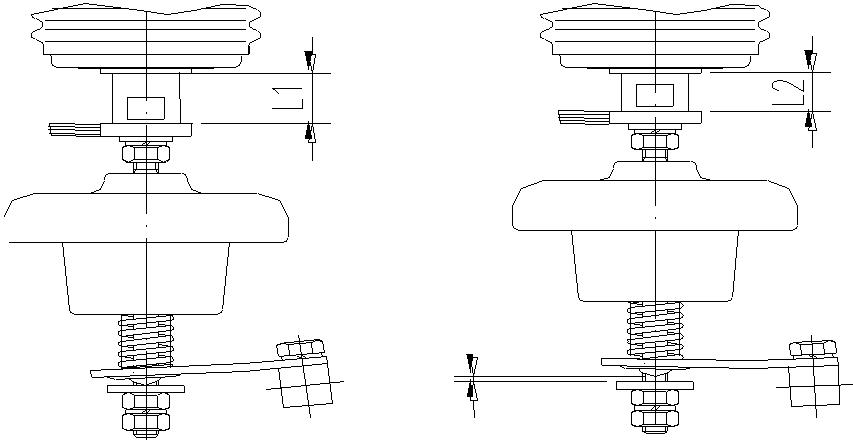
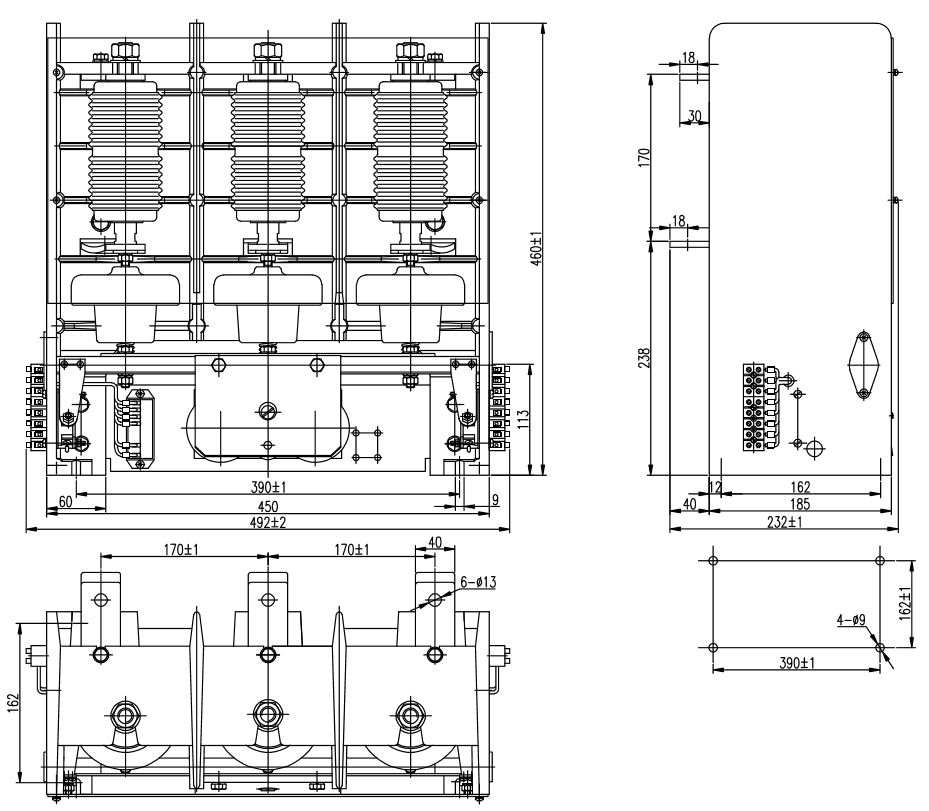
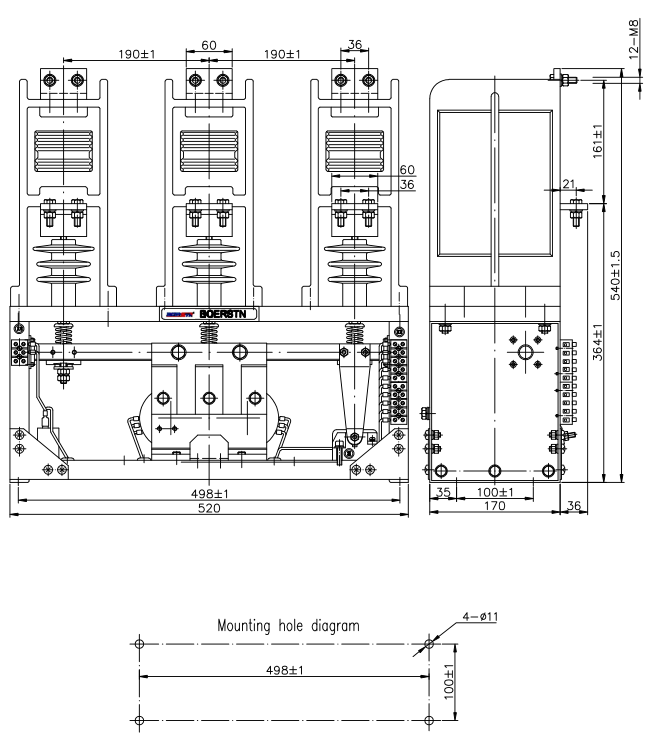
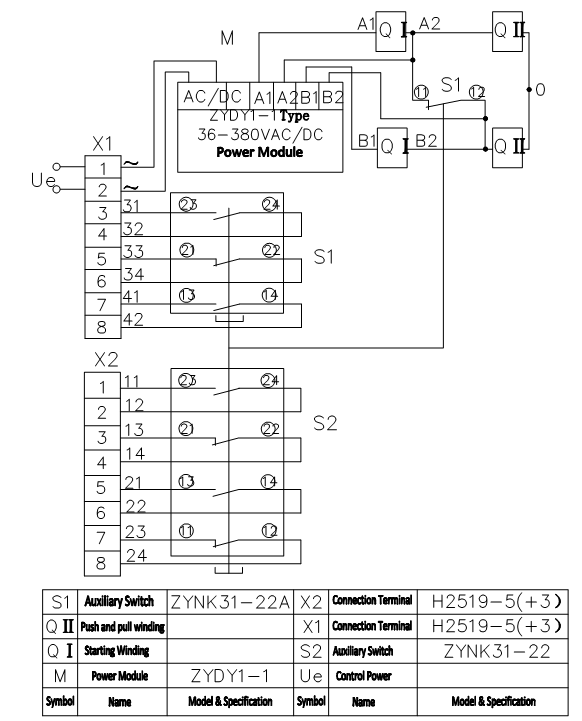



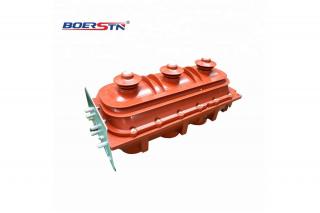